
(き裂発生と転位組織変化の非接触モニタリング)
1.はじめに
金属の疲労の研究は,最終的には耐疲労材料の開発あるいは余寿命評価につながるべきです.私達は後者を目指して電磁超音波計測を利用した研究を行ってきました[1-5]..ここでは主に,超音波減衰と音響非線型量を利用した鋼の回転曲げ疲労試験中に起こる内部組織変化のモニタリングと余寿命評価について紹介いたします.
電磁気力によって非接触で表面波を励起・検出することにより,材料に吸収される超音波エネルギ量(減衰)と波形のゆがみを表す非線型量を極めて高精度に計測することができます.非接触測定のため,疲労試験を中断することなく計測することも可能です.これらは伝ぱ領域内の平均的な転位組織変化やき裂の発生に敏感に反応します.鋼の回転曲げ疲労試験においては,破断寿命の6割付近に非線型量のピークが現れ,つづいて8割付近に減衰の鋭いピークが現れることを発見しました.組織観察の結果,それぞれ波長程度の長さのき裂の存在と固執すべり帯からセルへの転位組織変化を反映していることが明らかとなりました.ピークの発生時期は応力振幅(降伏応力の50-120%の範囲)と炭素量(0.22-0.45
mass%)に影響されないため,余寿命診断への適用が期待されます.
これらの成果は,イギリス物理機関(Institute of Physics: IOP)のweb雑誌,Physicswebで紹介され,また国内では産経新聞に掲載されました.
2.超音波と内部組織
2.1 非接触測定の重要性
意外に思われるかもしれませんが,「音」は金属の内部組織に敏感です.金属の鈴を鳴らすとやがて鳴り止みますが,これは,空気中に音のエネルギが漏れるためというよりはむしろ,金属内部で音のエネルギが消費されたためです.金属内部には転位や双晶などの格子欠陥が多く存在します.それらが擬弾性的に振動し,結果的に音のエネルギを熱に変換して消費してしまいます.実際にこの原理を利用した制振材料も存在します.周波数の高い音である超音波も同様に金属の内部組織に敏感です.ただし,超音波が伝ぱする領域にわたる平均の内部組織に対してであり,局所的に存在する一本の転位や一個の空孔などには感度がありません.しかし,一般に転位や空孔などの格子欠陥は金属中至る所に大量に存在するため,超音波によってこれらの形態の変化を検知することが可能となります.
金属の疲労においても内部組織の変化は顕著に起こります.その様子は材質や応力振幅などに依存しますが,必ず転位組織の変化とき裂の発生・進展を伴います.超音波によってこれらの組織変化を捕らえるためには,以下の2点を満足しなければなりません.
(1)表面波を使用する:疲労による組織変化は表面から起こり,また表面だけに限定される場合も少なくありません.材料全体を伝ぱするような超音波を使用すると,表面だけに起こる局所的な組織変化を検出することが困難となります.
(2)非接触測定を行う:超音波振動の様子を調べるために従来は接触式の計測法が用いられてきました.つまり,鳴り響いている金属に「触る」ことにより,振動を検出するのです.これは測定上の重大な欠陥です.例えば,鳴っている鈴の振動を測定しようとして指で軽く鈴に触れるとどうなるでしょうか?直ちに振動は鳴り止むことは容易に想像できます.これは振動のエネルギが指を通して鈴から漏れたためです.このように,振動体に接触して振動特性を計測するという試み自体が材料内の振動特性を著しくかき乱し,正確な計測を妨げるのです.
長い金属疲労の研究史においても,超音波特性を利用した研究は数多く存在しますが[6-9],上述の2点を満足した計測は行われてきませんでした.私達は電磁超音波共鳴[10]という計測法を開発し,これを実現することに初めて成功しました.超音波特性の中で,特に疲労損傷評価に有効と考えられるものは,「減衰」と「非線型量」です.前者は超音波が伝ぱする際にそのエネルギが転位の振動に費やされたりき裂によって散逸されたりして減少してゆく割合です.後者はき裂の開閉口や転位の振動によって超音波の波形が崩れてゆきますがその度合を表す無次元量です.
2.2 減衰と転位
転位まわりには高い応力場が存在します.超音波によって転位が安定位置から移動すると,応力場の急激な移動が起こり,これを妨げようとして熱弾性効果により発熱が生じます.これは不可逆過程であるため,超音波エネルギの一部が発熱に費やされます.このような超音波による転位の振動は,粘弾性体中の弦の振動としてモデル化され,減衰係数αと転位密度Λ,転位線長さLの関係を導くことができます[11].この関係は,比較的低い周波数領域では以下のように表すことができます.
α∝ΛL4 (1)
つまり,αは転位密度に比例し,転位線長さの4乗に比例します.ただし,注意すべきことは,式(1)が全ての転位を対象にしているわけではなく,超音波のような低応力波に対しても振動できる転位だけを対象としていることでです.したがって,結晶粒界や析出物などに強く拘束されている転位や,互いに強い相互作用で絡み合った転位などは振動することができませんから,αに貢献することができません.
2.3 非線型量とき裂・転位
金属材料では,音響非線型現象は原子間ポテンシャルの非調和性に加えて,転位振動などによる超音波エネルギの減衰に伴い,また微小き裂の開閉口によって発生します.Hikataら[12]は,転位の非弾性振動を調べ,2次高調波強度が転位密度とループ長さとともに増加することを示しました.また,わずかな圧縮応力によって閉口しているき裂が2次高調波源となることはMorrisら[13]によって示されています.したがって,疲労進行にともなって非線型量をモニタリングすることで,転位組織の変化およびき裂の発生時期を知ることが可能です.
3.電磁超音波共鳴
電磁超音波共鳴については文献[10]で詳しく紹介されています.基本的な原理は,電磁気的に超音波を送信し多重受信エコーを同位相で受信することにあります.電磁気的な計測は完全な非接触測定を可能としますが,送信・受信効率が悪いと言う点が欠点です.そこで,いくつもの超音波エコーを同位相にして強めあう状態(共鳴状態)を作って受信することで飛躍的に受信効率を増加させることに成功しました.
電磁気的な超音波計測には様々な手法が考案されていますが,ここでは鋼の磁わいを利用して,丸棒試料に表面波横波を励起する手法を用います.鋼のような強磁性体は磁化されると磁化方向にひずむ性質を持っています.このひずみを磁わいと呼びます.振動する磁場を印加すると振動するひずみが発生し,超音波音源となります.
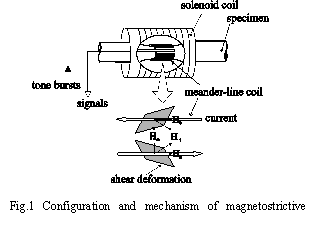 |
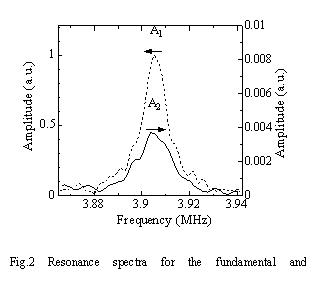 |
図1に示しますように,試料全周にわたってその表面付近に蛇行コイルを設置し,ソレノイドコイルによって試料軸方向に静磁場H0を印加します.この状態で蛇行コイルに長いバースト波電流を流して軸方向と直交する振動磁場Hωを試料表面に作ります.試料表面の合成磁場Htは,ソレノイドコイルの静磁場と蛇行コイルの振動磁場のベクトル和となり,軸方向からわずかに傾いた方向を向く.試料表面の磁わいはこの方向に発生します.隣り合う蛇行コイルの直下では,逆向きに傾いた合静磁場,すなわち逆向きの磁わいが発生します.この結果,せん断変形が生じ軸方向に偏向し周方向に伝ぱする表面波横波が発生します.このような表面波横波を軸対称SH波と呼びます.
軸対称SH波はすべての蛇行コイル直下から発生し,周方向に何周も伝ぱします.波長が蛇行コイルの周期と一致するときにすべての軸対称SH波は同位相となり,非常に強い振動が起こります.つまり共鳴するのです.蛇行コイルに流す電流の周波数を掃引することで発生するSH波の波長を変え,受信信号を測定すると図2の破線で示されるようなピークが観測されます.ピーク周波数が共鳴周波数です.
減衰係数は以下のように測定します.共鳴周波数でコイルを駆動すると,表面だけに強い振動振幅をもつ軸対称SH波の定在波を作ることができる.駆動を停止すると,定在波は時間とともに指数関数的に減衰してゆき,やがて振動が止まります.駆動の停止から定在波の振幅を測定してゆき,それが完全に零になるまでの変化(図3)を指数関数で近似すると減衰係数αが得られます.
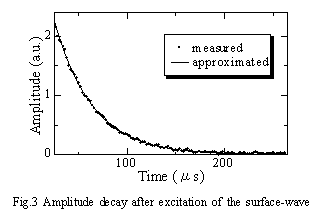
本研究では,第二次の高調波非線型量を測定しました.測定方法を以下に示します.まず共鳴周波数frでの振幅強度を測定し,これを基準振幅A1(fr)とします(図2).次に,入力電力を保持したまま半分の周波数fr/2でコイルを駆動し,周波数fr/2の軸対称SH波を発生させます.この周波数では共鳴条件を満足しませんが,非線型効果によって発生した2倍の周波数(fr)を持つ成分は共鳴するのでその振幅を測定します.これをA2(fr)とします(図2).
A2/A1を音響非線型量と定義して測定対象とした. A2/A1は1000分の1のオーダでした.
これらの超音波特性は,軸対称SH波の表面からの浸透深さにわたる組織変化に感度があります.浸透深さは使用する蛇行コイルの周期のおよそ2分の1です.私達は周期が0.9mmと0.44mmの2種類の蛇行コイルを用いました.したがって,それぞれ約0.45mmと0.22mmの浸透深さの軸対称SH波を発生させることができ,表面からこの深さまでの組織変化を評価することができます.コイルの軸方向の長さは20mmです.非線型量の測定には0.9mmのコイルだけを使用しました.
4.回転曲げ疲労試験
図4に回転曲げ疲労試験の様子を示します.炭素鋼丸棒(S25C,S35CおよびS45C)を880℃x1h焼鈍後に空冷して試料としました.長さは600mmであり,中央部で損傷が進行するよう半径を緩やかに変化させました.測定部位である中央での最小径は14mmです.測定面は電解研磨で仕上げました.4点曲げによる最大応力は,降伏応力の49-120%としました.回転速度は240rpm(4Hz)としました.適宜回転を停止し,除荷したのち音速(相対変化),減衰係数,非線型量を測定しました.また,レプリカ法で表面き裂の長さと密度を観察しました.以上の測定を破断するまで繰り返しました.
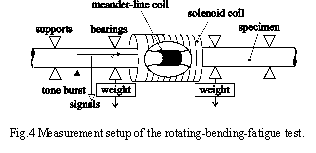
5.結果
無次元化した疲労回数N/NFに対する各測定量の典型的な変動を図5にまとめます
. き裂密度を全き裂長さ/全測定面積から計算し,視野内の最大き裂長さとともに図5(c)に示します.光学顕微鏡によりN/NF=0.3で長さ約50μmのき裂が観測されました.その後N/NF=0.7までき裂密度は急増しますが,最大長さはわずかに増加するだけでした.N/NF=0.7以降にこれらの微小き裂が結合してより大きなき裂になり破断に至りました.40本以上の試料に対して同様の測定を行いました.共通の観測事項を以下にまとめます.
(i) 減衰係数は末期にピークを示す.ピークの出現する時期は応力振幅と炭素含有量に依存しないが,使用する蛇行コイルの周期によってピークが出現する時期が異なる(図6).0.9mm周期の蛇行コイルでは寿命の85%で,0.44mm周期のコイルでは寿命の72%でピークが現れた.
(ii) 非線型量のピークが常に2度観測された.第一ピークは寿命の62%で現れ,第二ピークは寿命の85%で現れた.この割合は応力振幅と炭素含有量に依存しなかった(図7).
(iii) 第一ピークへ向けて非線型量が増加する傾向は,き裂密度の増加の傾向と類似した.
(iv) 同期して現れる減衰ピークと非線型量の第二ピークは,低温の加熱処理(300℃1時間)によって増加前の値に回復した(図8).また,図示していないが,減衰係数がピークを示したときに疲労試験を中断し,試料を室温で放置して減衰係数の測定を続けると,数十時間後に増加前の値まで減少した.
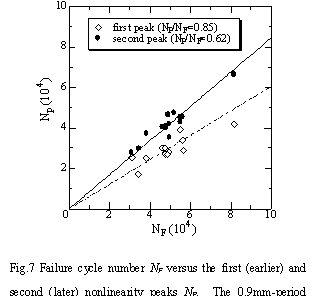 |
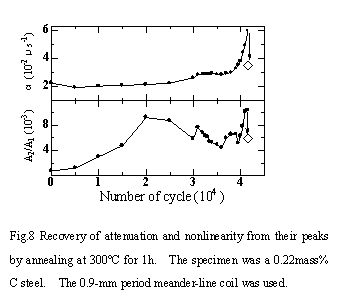 |
6.考察
まず,非線型量の第一ピークについて考えます.このピークはき裂密度の変化に相関があることから微小き裂の発生・成長を示しています.疲労によって発生した微小き裂では,塑性変形のため圧縮残留応力が生じ,き裂先端に沿う破面が一部閉じています[13].この領域の一部は,超音波の入射によって開閉して波形をゆがめるため強い非線型効果をもたらします.回転曲げ疲労によるき裂は扁平な半楕円形で,その大きさも比較的一様です.したがって,非線型量は微小き裂の発生数とともに増え,より大きいき裂への結合によって減少に転じます(完全に開口したき裂からは超音波の非線型性は生まれない).
次に,同期して発生する減衰および非線型量の第二ピークのメカニズムについて考察します.これらのピークが寿命と強い相関を示すことから,これらもき裂の発生・成長によって直接引き起こされたように思えます.しかし,この二つのピークが試料の低温加熱処理および室温時効によって消滅することから,き裂の直接的な関与は否定せざるを得ません.減衰や非線型量が熱処理や時効によって変化する場合,最も有力な要因は転位です.熱処理や時効によって転位は回復し,また転位周辺の点欠陥が転位に拡散して振動できる転位線長さが減少します.式(1)に示したように,転位密度および転位線長さの減少は減衰係数の減少をもたらします.非線型量も式(1)に似た関係を示すことが知られています[12].したがって,疲労末期の減衰および非線型量のピークは転位密度あるいは転位線長さが一時的に急上昇したことを示唆しています.
そこで,減衰ピークの発生前後で疲労試験を停止し,表面から0.15mmの位置(表面SH波の浸透している領域)での転位組織を透過型電子顕微鏡(TEM)によって観察しました.TEM観察では極めて局所的な情報しか得られないため,多数の試料について同様の観察を行い,減衰ピーク前後の代表的な内部組織を特定しました.結果を図9(a)-(c)に示します.
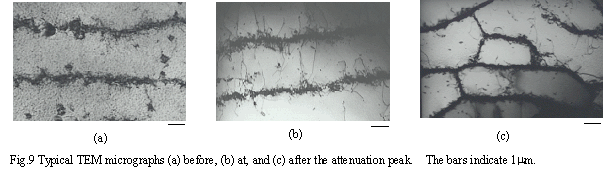
減衰ピークの前後で注目すべき転位組織の変化を確認することができました.ピーク直前には主に固執すべり帯(Persistent
Slip Band: PSB)[14]と思われる組織が観測されました(図9(a)).つまり,過度に密集した転位からなる転位壁がほぼ等間隔(約2μm)で並走し,転位壁間には孤立した転位はほとんど観察されませんでした.ところが,減衰ピークにおいては転位壁間を橋渡しするような転位が多数確認されました(図9(b)).減衰ピーク後には大きさが2-3
μmのセル組織が全体を占め,セル内の転位密度はかなり小さいことがわかります.このことから,減衰ピークの前後でPSBからセルへの急速な転位組織変化が生じたと考えられます.つまりPSBの転位壁を橋渡ししていた長い転位が集まって転位壁間を分割するようにセル組織へと移行していったことが推測されます.
PSBの転位壁やセル壁のように強い相互作用で堆積している転位は超音波によって振動できませんし,減衰には寄与しないでしょう.しかし,転位壁を橋渡ししている長い転位は超音波によって振動し,式(1)にしたがって超音波エネルギを吸収すると考えますと減衰ピークを説明することができます.つまり,疲労開始直後から転位密度は増加しつづけますが,ほとんどの転位は増殖するとすぐに結晶粒界や転位壁を作ってしまい,可動性を失います.しかし,ある時期に転位壁間を渡る長い可動転位が大量に発生し,これが超音波エネルギを吸収して減衰ピークや非線型量の第二ピークをもたらすのです.その後,すぐにこれらの転位は相互作用を起こして互いに引き合い,PSB組織を分割してセル壁を作ります.セル内には可動転位は存在しないため,超音波エネルギの吸収は収まり,減衰は再び低下するのです.
ここで注目していただきたいことは,減衰ピークは鋭く,寿命のわずか数%の間にだけ存在することです.つまり,上述したような組織変化は非常に短時間に起こり完了するのです.疲労にともなうPSBからセルへの組織変化は銅[15]や炭素鋼[16]においても過去に観測されていますが,いずれも十分なサイクル数と応力振幅が必要であることが示唆されており,このような短時間の組織変化はこれまで観測されたことがありません.私達が特に強調したいことは,疲労による組織変化を調べるにあたって疲労回数だけに注目していては決してこのように短時間に完了する組織変化を検知することができないということです.何故ならば,同一試料に対して同一条件で疲労試験を行ったとしても必ず大きな寿命のばらつきが生じるからです(このことは疲労の本質でもあり,また,このことがゆえに疲労研究が必要とされてきました).超音波減衰のように寿命と強い相関のある物理量を疲労試験中に非破壊かつ連続的にモニタリングすることで,初めて上述のような組織変化を観測することが可能となるのです.
減衰ピークや非線型量の第二ピークは寿命と強い相関がありますが,寿命を支配する直接的な因子はき裂であることは疑う余地がありません.ところが,すでに述べましたように,これらのピークは直接き裂によってもたらされたものではないのです.したがって,き裂が上述の組織変化に間接的に関係しているはずです.最後にこのメカニズムについて考察いたします.PSBからセルへの移行のためには十分に大きな応力振幅が必要であることが指摘されていますが[16],これはき裂先端近傍の応力集中領域において達成されると考えられます.実際図10に示すように,き裂先端近傍では減衰ピークの発生する前においても微小なセル組織を観測することができました.
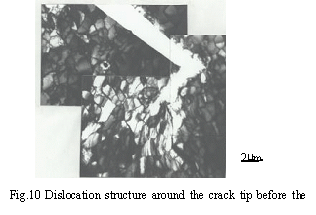
つまり,き裂先端の高い応力がPSBからセルへの組織変化の原因である.以上のことから図11に示すようなシナリオが考えられます.き裂は寿命の30%近辺から光学顕微鏡で観測できましたが,その長さは減衰ピークまで大きく変化せず100mm程度を維持しました.き裂形状は扁平半楕円形状でありき裂深さは数十μmと考えられます.これは使用している表面SH波の浸透深さ(200-500μm)よりも十分浅く,この段階でのき裂先端近傍の組織変化を捕らえることができないでしょう(図11の上図).しかし,き裂数は疲労とともに単調に増加するため,やがてき裂同士が結合して急激にき裂長さが増加します.き裂先端の応力集中係数はき裂長さとともに増加しますから,この段階でき裂は深さ方向へ進展します.これに伴い,高応力領域が深さ方向に広がり,表面SH波の伝ぱ領域の有為な体積を占めるようになります(図11の中央図).このとき,PSBからセルへの転位組織変化が伝ぱ領域内全域で起こり,PSB内の転位壁を橋渡しする長い転位が大量に発生して減衰の急上昇をもたらします.これらの転位はすぐにPSBを分割してセル組織を形成し,減衰は再び減少します.やがてき裂はさらに内部へ進展してゆき先端近傍の高応力領域は表面SH波の伝ぱ領域から外れます(図11の下図).したがって,より浅い浸透深さをもつ表面SH波を用いると,より早い段階で減衰ピークを観測することができます.このことは図6の結果を裏付けています.
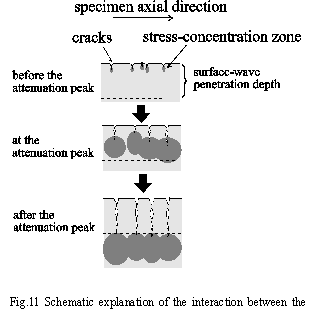 |
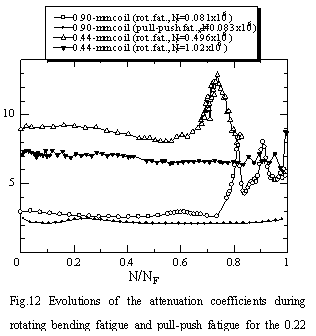 |
結局,減衰ピークを観測するためには超音波の伝ぱ領域内に多くのき裂が存在することが必要です.一本あるいは少数のき裂だけが発生・進展する場合には,減衰ピークを観測することができませんでした.例えば,図12は同一試料に対して回転曲げ疲労および両振り疲労にともなう減衰係数を同手法によってモニタリングした結果です.破断回数が回転曲げ疲労試験とほとんど同じであるにも関わらず,両振り疲労試験では減衰ピークが発生しませんでした.両振り疲労試験では,一本のき裂だけが発生し,それが早い段階から内部へ進展してゆき破断をもたらしました.したがって,表面SH波の伝ぱ領域に対してき裂が作る高応力領域は極めて局所的であり,その中で起こる組織変化を検知することができないのです.同様の結果は破断回数が百万サイクルを上回る回転曲げ疲労試験でも見られました.この場合も発生するき裂は数本であり,そのうちの一本だけが進展し破断をもたらしました.したがって,このような局所的にき裂が発生する場合に減衰ピークを検出するためには,蛇行コイルの軸方向長さを短くするなど,できるだけ超音波の伝ぱ領域をき裂近辺に絞る工夫が必要です.
7.おわりに
この測定の重要な点は,減衰係数や非線型量が材料の疲労過程を反映し最終的な破断に直接結びつく微視的特徴を検出できること,さらにそれらの変化が全疲労寿命のある特定の割合(寿命消費率)を再現性よく指し示めしていることです.これが実現した要因としては,(1)表面層を中心に進行する疲労損傷に対して浅い浸透深さの表面横波を利用したこと,(2)非接触の電磁超音波計測を用いたため,音響結合材や接触面の影響を受けることなく極めて正確な減衰係数や非線型量の計測が可能であったこと,の2点を挙げることができます.
参考文献
(1) H.Ogi et al, Metal. and Mater. Trans. A, 31A, pp. 1121-1128 (2000).
(2) M. Hirao et al, Acta Materialia, 48, pp. 517-524 (2000).
(3) H. Ogi et al, J. Alloys and Compounds, 310, pp. 436-439 (2000).
(4) H. Ogi et al, J. Appl. Phys., 90, 438-442 (2001).
(5) H. Ogi et al, J. Appl. Phys., 91, (2002), in press.
(6) W. J. Bratina, in Physical Acoustics IIIA, W. P. Mason, ed., Academic
Press, New York, NY, 1966, pp. 268-291.
(7) R. Truell and A. Hikata, ASTM-STP 213, ASTM, Philadelphia, PA, 1957,
pp. 63-70.
(8) G. Fei and Z. Zhu, Phys. Status Solids (a), 140, pp. 119-126, (1993).
(9) Z. Zhu and G. Fei, J. Alloys Compounds, 211-212, pp. 93-95, (1994).
(10) M. Hirao and H.Ogi, Ultrasonics, 35, pp. 413-421 (1997).
(11) A. Granato and K. Lucke, J. Appl. Phys., 27, pp. 583-593 (1956).
(12) A. Hikata et al, J. Appl. Phys., 36, pp. 229-236 (1965).
(13) W. L. Morris et al, J. Appl. Phys., 50, pp. 6737-6741 (1979).
(14) S. Suresh, Fatigue of Materials, 2nd edition, Cambridge University,
Cambridge, 1998.
(15) H. Mughrabi et al, In Fatigue Mechanism, STP 675, pp. 69-105, 1979,
Philadelphia, ASTM.
(16) K. Pohl et al, Scripta Metall., 14, pp. 1167-1169, (1980).